Structural Audit for Safe Facilities in Your Supply Chain
Ensure structural safety of factories and facilities within your supply chain and compliance with building codes and safety standards.
QIMA's structural audit involves a thorough examination of the structural components of a building in your supply chain. This may involve visual inspection, non-destructive testing, and sampling materials for analysis. The audit evaluates the condition of the structure by identifying cracks, corrosion, water damage, wear, and other important factors.
Read on to learn more about:
What is a Structural Audit?
QIMA's Solution
QIMA's Structural Audit Protocol
The Next Steps after a Structural Audit is Completed
Follow-Up Services
Why Perform a Structural Audit?
QIMA Benefits
Need more information?
By contacting QIMA you agree to our privacy policy and terms and conditions.
What is a Structural Audit?
A structural audit is the first step in identifying structural safety risks and implementing preventative measures to safeguard the lives of those working in factories and other facilities within your supply chain.
Since the Rana Plaza disaster in 2013, awareness of the lack of structural safety in many factory facilities, particularly in developing countries, has significantly increased. Tragically, structural safety failures continue today, with all-too-regular reports of factory fires, explosions, and collapses. More often than not, these tragedies would have been prevented if regular checks and maintenance had been carried out.
Several factors can increase the risk level in factory facilities, including:
Extreme weather, such as monsoon rains or heavy snowfall
Natural events, such as earthquakes
Vibration caused by machinery or construction work in the area surrounding a building
Water leaks in walls
Structural additions, such as mezzanine floors or additional storage areas
Heavy loads, such as the addition of water storage tanks on building roofs, floor storage & racks
Exposure to corrosive chemicals
Repurposing of a building to serve a different function to what it was designed for
Create an account and book a structural audit here
QIMA’s Solution
QIMA provides comprehensive structural audits to ensure your suppliers' industrial and commercial facilities are structurally sound, compliant with building codes, and safe for employees.
Our audits are conducted by licensed, highly experienced structural engineers with expertise in design and construction supervision. Partnering with QIMA for structural inspections provides you with peace of mind and confidence in your supply chain.
QIMA’s Structural Audit Protocol
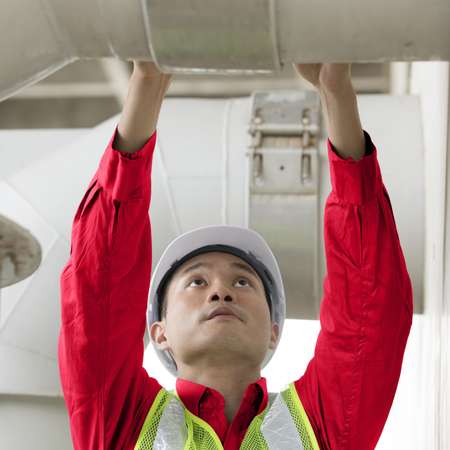
Our audit protocol covers:
Background information/documentation: Detailed building description, verification of structural certifications and construction approvals
Load conditions: Floor-by-floor assessment of load management, identification of 'at risk' loads and misuse of the building; application of non-destructive testing (NDT).
Structural system: Description of structural forms and the building foundation system, review of alterations
Structural defects, damage, distress, deformation, or deterioration: Foundations, superstructure, floors, and roof assessment
Plan and alignment: Verification that dimensions in key areas of the factory comply with the design plan.
Building maintenance and exposure to aggressive environmental conditions: Evaluation of building maintenance, drainage, and exposure to chemicals that could affect structural safety
Further structural surveys and checks: Additional assessment of potentially dangerous structural features, such as water tanks, lifts, and safety barriers
Fire safety: Full verification of fire safety compliance based on local legal requirements and best practices in the industry
Electrical safety: Full verification of electrical safety compliance, based on local legal requirements and best practices in the industry
Thermographic scan: Verification of the temperature of key electrical components to identify potential risks related to overload or loose connections.
The Next Steps After a Structural Audit Is Completed
Post-audit, we will provide a comprehensive structural audit report, accessible through your online QIMA account.
The report includes:
Grading of the factory’s safety level
Detailed explanation of any identified risks
Necessary supporting photographic evidence
Our auditor will also provide a corrective action plan, based on the audit findings, which will detail any necessary remediation steps, such as repairs, retrofitting measures, strengthening of structural elements, or replacement of damaged or faulty components.
Follow-Up Services
Beyond the audit, we also assist factories in addressing potential risks. We can help establish an improvement program for each factory andprovide follow-up to ensure that the necessary corrective actions are implemented.
We can also provide other follow-up services, such as:
Live load analysis through laboratory material testing and/or on-site stress tests
Post-earthquake inspection
Simulation performance testing
Fire safety and electrical plan redesign
Review of geotechnical reports to support factories in their remediation efforts
Custom onsite training, eLearning, and workshops on structural safety best practices and specific structural safety topics, such as load analysis and fire safety.
These combined services help suppliers achieve structural safety compliance.
Why Perform a Structural Audit?
A QIMA structural audit will ensure that working conditions in your supplier’s factory facilities are safe.
Use our structural audit to:
Ensure safe working conditions and prevent injury and loss of life
Gain an accurate picture of the current conditions in your supplier’s buildings
Identify critical areas that require immediate action
Extend the life of buildings through preventative and corrective measures such as repairs and retrofitting
Comply with statutory requirements, including construction and design codes specific to each country
Create an account and book a structural audit
QIMA Benefits
In-depth local knowledge with auditors attuned to the culture, laws and practices of their region.
CSR experts receive regular training on regulations and best practice.
Global coverage across 100 countries in Asia, Africa, Europe, North and South America.
Continuous improvement approach drives long-term change and empowers suppliers to act.
Online program management book audits, make payments, and download detailed reports.
Custom compliance dashboard to assess supplier performance, track progress and visualize your supply network.
Ranked #1 in the industry for customer satisfaction based on independent NPS measurement.